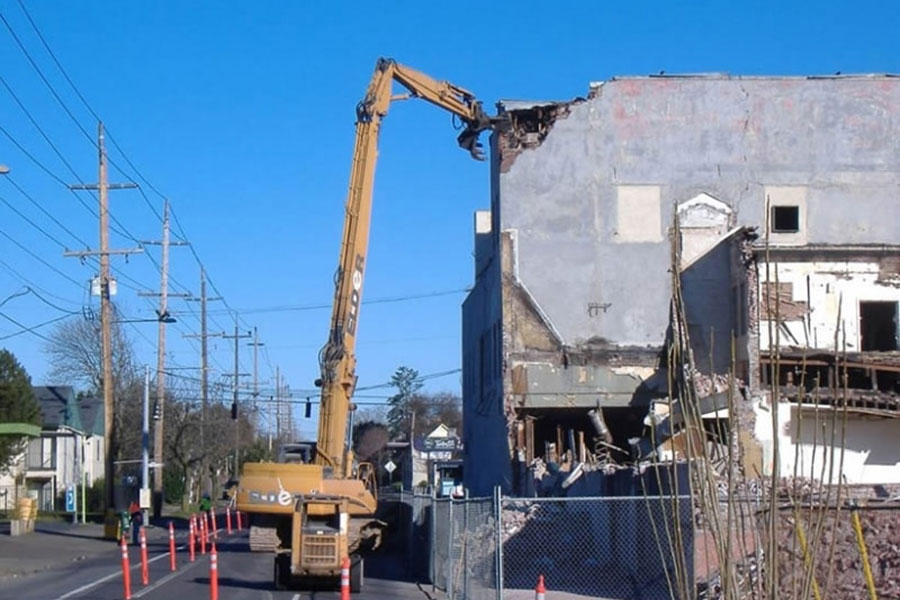
In industrial demolition, long-reach excavators are used when explosives aren't an option or when workers deconstruct a building piece-by-piece; long-reach excavators provide the precision and control that wrecking balls don't offer.
Their versatility as a demolition tool is incomparable – while it's common to see an excavator with a bucket at the end of its 20- to 150-foot arm, a contractor may also replace the bucket with a shearing, crushing, or cutting implement to enhance the efficiency of industrial and scrap metal demolition projects.
Long-Reach vs. High-Reach Excavators
Two types of excavators can reach great lengths: the long-reach excavator and the high-reach excavator. Long-reach excavators extend horizontally but not vertically, while high-reach excavators do the opposite. The long-reach excavator is ideal for scrap metal demolition because it can reach a site and scoop up rubble. In contrast, the high-reach excavator allows workers to be farther away from falling debris.
Benefits of Long-Reach Excavators
Increased precision
Operators have more control over the movements of a high-reach excavator. With a wrecking ball, the technique is "aim and swing." On the other hand, Excavators allow contractors to demolish a building wall-by-wall or a floor at a time.
Increased safety
Because these excavators offer more precision than a wrecking ball, contractors have more control over how and where the debris falls. This practice creates a safer environment for workers, surrounding buildings, and the public.
Attachments
The attachments you can add to a long-reach excavator make it a versatile machine that can use the hammer, pinch, pick, crush, scoop, cut, and more – thus eliminating the need to transport several pieces of heavy machinery. Also available is the option to change the arm's length so a contractor can efficiently switch to an alternative demolition method.
Fuel efficiency
In addition to releasing less particulate matter in the exhaust, long-reach excavators have no exhaust gas recirculation (ERG) on the engine, reduced fuel consumption of up to 24 percent, and a machine that automatically revs less when the controls are inactive.
Long-Reach Excavator Attachments: Grapples and Electromagnets
Grapples
A grapple attached to an excavator's end allows scrap metal demolition workers to lift different materials based on size, shape, and composition. Manufacturers often provide a lift chart describing the machinery's lifting and hydraulic capabilities and the attachments offered. Common types of grapples include the orange peel and clamshell.
Orange peel grapples look like the metal claws in the "claw crane" arcade game, where you test your luck to grab a stuffed animal. However, instead of having three fingers or lines, an orange peel grapple has four or more. This type of grapple's gripping power is powerful because of the clamping force of the heavy-duty cylinders.
An orange peel grapple has a 360-degree, bi-directional rotation system that makes it ideal for picking up structural beams, car bodies, shredded scrap, and other types of debris with precision and ease. Orange peel grapples are an excellent go-to option for general purposes.
Clamshell grapples resemble an eagle's foot and nails, with three tines on one side and two on the other. Contractors can custom design the grapple's head for their particular purposes. It's common for clamshell grapples to come with plumbing packages and other features designed for rugged demolition.
Scrap Electromagnets
A grapple with an integrated electromagnet prevents the need to change an excavator's attachments frequently. After the operator finishes the production part of an industrial demolition project, they can use the magnet for smaller items and cleanup. A contractor may use a lifting or scrap magnet in scrap metal demolition.
Lifting magnets can be as small as credit cards or larger than beds. They're generally attached to a chain on the end of an excavator or crane to safely and quickly pick up smaller pieces of scrap metal. Lifting magnets are ideal for getting into hard-to-reach, unstable, or dangerous areas.
Contractors use scrap magnets to lift heavy metal objects like cars or beams, which work well in constricted areas and have an extra-deep magnetic field. A contractor may have a scrap magnet explicitly made for wet conditions, detecting radiation, or hot applications.
The long-reach excavator is the answer to safer, more precise industrial and scrap metal demolition. This modern machine accommodates the most challenging demolition projects with advanced features like camera monitoring, controlled hydraulic systems, boom extensions, and more.